方形铝壳锂电池具有结构简单,抗冲击性能好,能量密度高,单体容量大等诸多优点,一直以来都是国内锂电制造和发展的主要方向,市场占比在40%以上。
方形铝壳锂电池结构如图1,由电芯(正负极片、隔膜)、电解液、壳体、顶盖等部件组成。
方形铝壳锂电池在制造组装过程中,需要大量应用到激光焊接工艺,例如:电芯软连接与盖板焊接、盖板封口焊接、密封钉焊接等等。
激光焊接是方形动力电池的主要焊接方法,归功于激光焊接具有能量密度高,功率稳定性好,焊接精度高,易于系统化集成等诸多优点,在方形铝壳锂电池生产工艺中,有不可替代的作用。
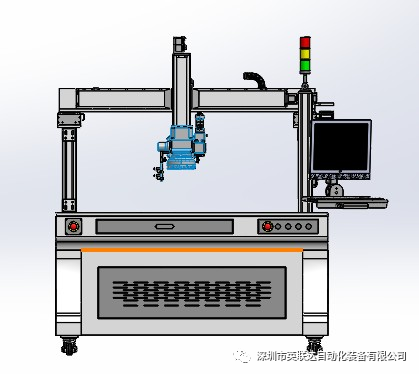
附:英联达3000w龙门连续振镜激光焊接机
顶盖封口焊接焊缝是方形铝壳电池中尺寸最长的焊缝,也是焊接耗时最长的焊缝。近年来锂电制造行业高速发展,顶盖封口激光焊接工艺技术及其装备技术也在快速发展,我们根据装备的焊接速度性能不同,将顶盖激光焊接设备及工艺大概划分为3个时代。
分别是焊接速度<100mm/s的1.0时代(2015-2017),100-200mm/s的2.0时代(2017-2018),以及200-300mm/s的3.0时代(2019-)。下文将沿着时代路径介绍技术的发展:
2015-2017年,国内新能源汽车受政策驱动,开始爆发,动力电池行业开始扩张,但国内企业技术沉淀、人才储备还相对较少,相关电池制造工艺和装备技术也在起步阶段,设备自动化程度相对较低,设备制造商刚开始关注动力电池制造并加大研发投入。
在此阶段,行业内对方形电池激光封口设备的生产效率要求通常在6-10PPM,设备方案通常使用1kw光纤激光器通过普通激光焊接头出射(如图2),由伺服平台电机或直线电机带动焊接头运动并进行焊接,焊接速度50-100mm/s。
在激光焊接工艺上,也正由于焊接速度相对较低,焊缝热循环时间相对较长,熔池有足够的时间流动和凝固,且保护气体能较好的覆盖熔池,易获得表面光滑饱满、一致性好的焊缝,如图3。
在设备上,虽然生产效率不高,但设备结构相对较简单、稳定性较好且设备造价低,很好的满足了该阶段行业发展的需求,为后续技术发展打下了基础。
顶盖封口焊1.0时代虽然有设备方案简单、成本低、稳定性好等优点。但是其固有的局限也十分明显。设备上,电机驱动能力不能满足进一步提速的需求;
工艺上,单纯通过提高焊接速度、激光功率输出来进一步提速会带来焊接过程的不稳定和良率的下降:提速使得焊接热循环时间缩短,金属的熔化过程更剧烈、飞溅加大、对杂质的适应会更差,更易形成飞溅孔洞,同时熔池凝固时间的缩短,会导致焊缝容易表面粗糙、一致性降低。
当激光光斑较小时,热输入量不大,飞溅可以降低,但焊缝深宽比较大,焊缝熔宽不够;当激光光斑较大时,需要输入较大的激光功率,使焊缝宽度增大,但同时又会导致焊接飞溅增加,焊缝表面成型质量差。
在该阶段的技术水平之下,进一步的提速意味着需以良率换效率,装备和工艺技术的升级要求成为行业性需求。
2016年中国汽车动力电池装机量约30.8GWh,2017年约36GWh,而2018年迎来了进一步的爆发,装机量达到57GWh,同比增长57%,新能源乘用车也生产近百万量,同比增长80.7%。
装机量爆发的背后是锂电制造产能的释放,新能源乘用车电池装机占比超50%,也意味着行业对电池性能、质量的要求会越来越严格,随之提升的制造装备技术及工艺技术也进入了新的时代:
为了满足单线产能要求,顶盖激光焊接设备需要产能提升到15-20PPM,其激光焊接速度需要达到150-200mm/s,所以在驱动电机上,各设备厂商均升级了直线电机平台,使其运动机构满足对矩形轨迹200mm/s匀速焊接的运动性能要求;
但针对高速焊接情况下如何保证焊接质量,需要进一步工艺突破,行业内企业进行了诸多探索和研究:
相对1.0时代,2.0时代高速焊接所面临的问题是:采用普通的光纤激光器通过普通焊接头输出单点光源的方案,选型很难满足200mm/s的要求。
在原有技术方案上,只能通过配置选项,调整光斑大小,以及调整激光功率等基本参数来控制焊接成型效果:采用光斑较小的配置时,焊接熔池匙孔细小,池形态不稳定,焊缝熔宽也偏小;而采用光斑较大的配置时,匙孔会增大,但是焊接功率显著的提高,飞溅和爆孔率显著提高。
从理论上,如果想保证顶盖高速激光焊接的焊缝成形效果,需要满足以下一些要求:
①焊缝具有足够的宽度,且焊缝深宽比合适,这就需要光源的热作用范围足够大,且焊接线能量在合理范围;
②焊缝光滑,这需要焊缝在焊接过程中热循环时间足够长,使熔池具有足够的流动性,在保护气的保护下焊缝凝固成为光滑的金属焊缝;
③焊缝一致性好、气孔、孔洞少,这需要焊接过程中,激光稳定的作用于工件上,高能束等离子体持续的产生,作用于熔池内部,熔池在等离子反作用力下生产“匙孔”,匙孔足够大且足够稳定,使得生成的金属蒸汽和等离子体不易喷射和带出金属熔滴,形成飞溅,匙孔周围熔池也不易坍塌,卷入气体。
即便焊接过程中遇异物烧损,爆炸式的释放气体,更大的匙孔也更利于爆炸性气体的释放,减小金属飞溅和形成的孔洞。
针对以上的几点,行业内的电池制造企业、设备制造企业都进行了各种尝试和实践:
锂电制造在日本发展已有几十年,相关制造技术上先行一步。从相关公开专利可以搜索到,十余年前,日本松下株式会社就为了解决在激光焊接-铝这样的高反射金属时,熔深、熔宽及焊接速度都不够的问题,研究了不同波长、光学特性的多种激光混合输出进行焊接的技术。
在光纤激光器技术尚未大量商业应用的2004年,松下公司采用LD半导体激光与脉冲灯泵浦的YAG激光器进行混合输出(方案如图4所示)。
利用光斑较小的脉冲YAG激光器产生的高功率密度光斑作用于工件,生成焊接小孔,以获得足够的焊接熔深,同时用LD半导体激光器提供CW连续激光,对焊接的工件进行预热、对焊接过程中的熔池提供更多能量以获得较大焊接小孔、增大焊缝宽度,并延长焊接小孔闭合时间,帮助熔池气体逸出,降低焊缝气孔率,如图5。
应用该技术,使用仅有几百瓦功率YAG激光器和LD激光器,即可对薄壳体的锂电池壳体进行80mm/s的高速焊接,焊接效果如图6。
随着光纤激光器发展和兴起,光纤激光器凭借其光束质量好、光电转换效率高、寿命长易维护、功率高等诸多优点,逐步大量取代了脉冲YAG激光器在激光金属加工中的应用。
因此,以上的激光复合焊接方案中的激光器组合演化为光纤激光器+LD半导体激光器,并同样通过特殊加工头同轴输出激光(焊接头如图7),其焊接过程中,激光作用机理相同。
该方案中,将脉冲YAG激光器更换为光束质量更好、功率更大、并且可以连续输出的光纤激光器,大大提高焊接速度,同时获得较好的焊接质量(焊接效果如图8),该方案也因此受一些客户的青睐,目前该方案已经应用在动力电池顶盖封口焊的生产中,可达到200mm/s的焊接速度。
虽然双波长激光焊接方案解决了高速焊接的焊缝稳定性,满足了电芯顶盖高速焊接的焊缝质量要求,但是从设备和工艺的角度上,该方案也还存在一些问题。
首先,该方案硬件组成部分较为复杂,需要用到两台不同类型激光器以及特殊的双波长激光焊接头,提高了设备投入成本、增大了设备维护难度,设备潜在故障点增多;
第二,采用的双波长激光焊接头,由多组镜片组成(见图4),功率损耗较普通焊接头要大,且需要将镜片位置调节至合适位置,以保障双波长激光同轴输出、并聚焦在固定的焦平面上,长期高速运行,镜片的位置可能松动导致光路变化、影响焊接质量,需要人工再调试;
第三,焊接时,激光反射较严重,易损伤设备器件,特别是对不良品进行返修时,光滑的焊缝表面对激光进行大量反射,易造成激光器报警,需要调整加工参数进行返修。
为解决以上问题,得另辟蹊径,进行探索,在2017-2018年研究了电芯顶盖的高频摆动激光焊接技术并推进到生产应用。激光束高频摆动焊接(以下简称摆动焊接)是目前200mm/s高速焊的另一种工艺。
相对于复合激光焊接方案,该方案硬件部分只需要一台普通光纤激光器,搭配一台摆动激光焊接头(如图9 IPG wobble摆动焊接头)。
焊接头内部具有受电机驱动的反射镜片,可由程序控制激光按照设计的轨迹类型(通常有圆形、S形、8字形等)、摆幅及频率进行摆动,不同的摆动参数,可以使焊接截面呈不同形状及不同尺寸(如图10)。
高频摆动焊接头在直线电机的带动下沿工件间隙进行焊接,根据电芯壳体壁厚,选择合适的摆动轨迹类型及幅度,焊接时,静态的激光束只会形成V字形焊缝截面,但在摆动焊接头的驱动下,光束斑点在焦平面上高速摆动,形成一个动态的、旋转的焊接匙孔,可获得合适的焊缝深宽比;
旋转的焊接匙孔搅拌焊缝一方面帮助气体逸出减少了焊缝气孔,且对焊缝爆点针孔有一定修复作用(见图12),另一方面焊缝金属的有序受热-冷却循环让焊缝表面呈规则有序的鱼鳞纹。
以上几点,满足了顶盖高速焊接焊缝的三点基本质量要求,该方案还有其他优点:
①由于激光功率大部分注入到了动态匙孔中,对外散射激光减少,所以只需用较小的激光功率,焊接热输入量相对较低(比复合焊接减少30%),减少了设备损耗及能源损耗;
②摆动焊接方式对工件装配质量适应性较高,减少了装配台阶等问题造成的不良;
③摆动焊接方式对焊缝孔洞具有极强的修复作用,使用该方案修复电芯焊缝孔洞良率极高;
随着新能源补贴的不断退坡,电池制造行业几乎整个产业链陷入一片红海,行业也进入洗牌期,规模和技术优势的龙头企业所占比重进一步增加。但与此同时,“提质、降本、增效”将会成为很多企业主旋律。
在低补贴或无补贴时期,只有实现技术的迭代升级,实现更高的生产效率,降低单个电池的制造成本、提高产品品质,才能在竞争中多一分胜算。
大族激光在电芯顶盖高速焊接技术上,继续保持研究投入,除以上介绍的几种工艺方法,还研究了电芯顶盖的环形光斑激光焊接技术及振镜激光焊接技术等先进技术。
为了进一步实现生产效率的提高,探索300mm/s及更高速的顶盖焊接技术。大族激光在2017-2018年研究了扫描振镜激光焊接封口,突破了振镜焊接时工件难以进行气体保护,焊缝表面成形效果差的技术难点,实现电芯顶盖400-500mm/s的激光焊接,对一个26148电池只需1秒钟。
但由于效率过高,与其匹配效率的配套设备开发难度极大,设备成本较高。故对该方案,未做进一步商业化应用开发。
光纤激光器技术进一步发展,TRUMPF、nLIGHT、Coherent-Rofin、IPG等激光器公司,纷纷推出了可直接输出环形光斑的新型高功率光纤激光器,该类型激光器通过特殊的多层光纤,可输出点-环形激光光斑,并且光斑形状及功率分布可调节,如图13。
通过调节,可使激光功率密度分布呈点-环-帽形(spot-donut-tophat),nLIGHT公司也形象的把他们的这类激光命名为Corona(日冕),图14。
图14 可调节激光的光束(分别为:中心光,中心光+环形光、环形光,两个环形光)
我们在2018年也测试了多台该类型激光在铝壳电芯顶盖焊接上的应用,并以Corona激光器为基础,展开了电芯顶盖激光焊接的3.0工艺技术方案的研究。Corona激光器在进行点-环形模式输出时,其输出光束的功率密度分布特性类似半导体+光纤激光器的复合输出。
在焊接过程中,具有高功率密度的中心点光起到形成匙孔进行深熔焊,获得足够的焊接熔深(作用于复合焊方案中的光纤激光器输出类似),环形光提供更大热输入、增大匙孔,减少金属蒸汽、等离子体对匙孔边缘液态金属的冲击,降低由此造成的金属飞溅,并增长焊缝热循环时间,帮助熔池中气体有更长时间逸出,提高高速焊接过程的稳定性(作用类似于复合焊方案中的半导体激光器输出)。
在试验中,我们焊接了薄壁壳体电池,发现其焊缝尺寸一致性较好,具有较好的过程能力CPK,如图18。
图18 壁厚0.8mm的电池顶盖焊外观(焊接速度300mm/s)
在硬件方面,不同于复合焊方案的是,该方案简单,不需要两台激光器,不需要特殊的复合焊接头,只需要一个常见的普通高功率激光焊接头(由于只有一根光纤输出单一波长激光,镜片结构简单、无需调节、功率损耗低),使其调试和维护简单,其设备的稳定性极大的提高。
除了硬件方案上系统简单、满足电芯顶盖高速焊接工艺需求以外,该方案在工艺应用上还有其他优点。
试验中,我们在300mm/s的高速度下对电芯顶盖进行焊接,仍然获得了良好的焊缝成形效果,并且,对于0.4、0.6、0.8mm几种不同壁厚的壳体,只需通过简单的调节激光输出模式,即可良好的进行焊接,而对于双波长激光复合焊接方案,则需要变更焊接头或激光器的光学配置来实现,并带来较大的设备成本和调试时间成本。
因此,点-环形光斑激光焊接方案不但能实现300mm/s的超高速顶盖焊接,提高动力电池的生产效率,对于需要频繁换型的电池制造企业,该方案还能极大的提高设备对产品的兼容性、缩短换型调试时间。
图16 壁厚0.4mm的电池顶盖焊外观(焊接速度300mm/s)
图17 壁厚0.6mm的电池顶盖焊外观(焊接速度300mm/s)
图19 Corona激光器对薄壁电池焊接的焊缝熔深-过程能力
除以上提及的nLIGHT公司的Corona激光器,IPG公司推出的AMB激光器、Coherent-Rofin公司推出的ARM激光器均有类似的光学输出特性,可应用于解决诸如:改善激光焊缝飞溅、改善焊缝表面质量、提高高速焊接稳定性等问题。
以上提及的多种方案,均在国内外锂电制造企业中应用于实际生产,由于投产时间不同、技术背景不同而选择了不同的工艺方案在行业中广泛存在,但企业对效率、质量的要求是不断提高的,更多新的技术会很快被走在技术前沿的企业所应用。
中国新能源电池行业相对起步较晚,在国家政策驱动下飞速发展,相关技术在全产业链共同努力下不断进步,全面缩短与国际优秀企业差距。作为国内锂电设备制造商,深圳英联达也在不断挖掘自己的优势领域,帮助电池pack设备迭代升级,为新能源储能电池模组pack自动化生产提供更优质的解决方案。
参考资料:深圳市英联达
2021年全球电化学储能装机规模21.1 GW。其中,锂离子电池93.9%;铅蓄电池2.2%;钠基电池2.0%;液流电池1.2%;超级电容器0.2%;其它0.5%。到2025年,预计电化学储能增量将达到12GW/年,累计装机约40GW。在储能产业链中,各种电化学储能技术、新材料、先进制造设备、储能配套设施等都迎来了爆发式增长的机会。为促进储能产业行业交流,艾邦特建有“储能产业交流群”,欢迎业内人员加入。
方法:长按识别二维码关注公众号,点击公众号下方菜单栏“微信群”,申请加入群聊。
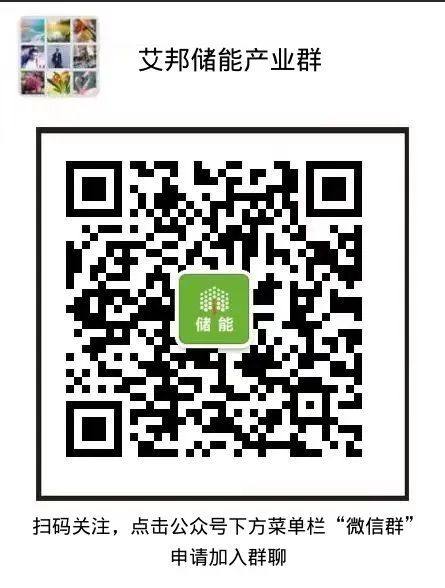
活动推荐
7月20日(周四):14:00~18:00签到
7月21日(周五):7:30~8:50签到;8:50~18:00会议
序号
|
议题
|
1
|
储能行业发展概况及储能电源生产工艺流程 |
2
|
储能PACK整线自动化解决方案 |
3
|
激光焊接在储能电源生产中的应用 |
4
|
激光切割/清洗/打标等在储能PACK上的应用 |
5
|
AI视觉检测在储能PACK的应用 |
6
|
电池组综合测试系统/整机老化柜的重要作用 |
7
|
储能电池包的热管理系统设计 |
8
|
储能电池包的电池管理系统(BMS)设计 |
9
|
新型户用储能逆变器PCS的开发应用 |
10
|
电子元器件在储能电源上的应用 |
11 |
钠离子电池在储能领域的应用前景 |
12
|
全钒液流电池在储能领域的应用前景 |
13 |
锂硫/锌铁等新型电池技术在储能上的应用 |
14
|
工程塑料在储能PACK的应用 |
15
|
防火隔热材料在储能PACK的应用 |
16
|
储能电池包的粘接与密封 |
17
|
导热散热材料在储能的应用 |
18
|
便携式储能的CMF设计 |
★如需演讲,请联系艾可13312943232(同微信)
方式1:加微信并发名片报名
扫描二维码加微信
肖小姐:13684953640(同微信)
邮箱:ab012@aibang.com
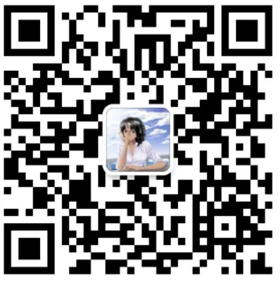
方式2:在线登记报名
报名链接:或者识别二维码进入报名页面登记信息https://www.aibang360.com/m/100158?ref=172672
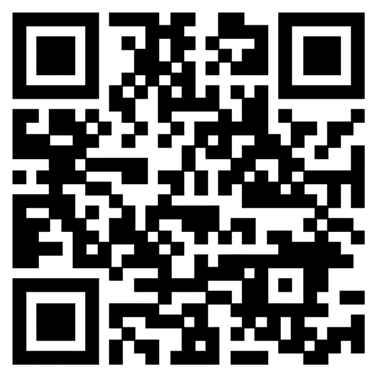
注意:每位参会人员都需要登记信息
原文始发于微信公众号(艾邦储能与充电):铝壳电池激光焊接技术的发展史