液流电池主要因为其可扩展性,可突破锂离子电池在电力系统中在储能时长方面的限制,用于长时储能,因此在电力系统中具有一定的发展空间。其中全钒液流电池目前产业链建设和技术成熟度相对较高。因此钒的提取有重要价值。
在自然界中,钒分布比较分散,主要与其他矿物、原油、煤等共生,主要的提钒原料有钒钛磁铁矿、石煤、矿渣、石油、沥青等,其中世界上钒年产量的80%是从钒钛磁铁矿中获得的。
目前,从钒钛磁铁矿提钒主要有直接提钒与间接提钒,间接提钒又分为钒渣提钒与含钒钢渣提钒。
一、钒钛磁铁矿直接提钒
钒钛磁铁矿是主要的提钒原料,对于高钒钛、低铁型的钒钛磁铁矿(V2O5质量分数大于1%)采用先提钒后回收钛、铁的工艺流程。
钒钛磁铁矿直接提钒工艺,是以钒钛磁铁矿精矿为原料,与添加剂混合后氧化焙烧,然后浸出,接着沉钒,钒作为主要产品,钛、铁为副产品产出。
主要提钒工艺有两种,分别为钠化焙烧-水浸提钒与钙化焙烧-碱浸提钒。
钒钛磁铁矿提钒工艺流程
-
1.钒钛磁铁矿钠化焙烧-水浸提钒
-
该工艺操作简单,因无炼铁、吹炼的消耗,钒的损耗较小,钒回收率高,一般来说钒回收率可达到80%以上,与此同时也可以回收钛、铁。但是由于物料处理量大,焙烧耗时长易粘结,能耗高,产生废水量大,因此难以实现大规模生产,还需要逐渐优化方案,改进提钒工艺。
2.钒钛磁铁矿钙化焙烧-碱浸提钒
据资料显示,对钒钛磁铁矿精矿进行钙化焙烧-浸出提钒,以10%的CaCO3为焙烧剂,在1200℃的焙烧温度中焙烧1h,钒的转化率达到了72.1%。该工艺在焙烧过程中不产生有害气体,废水循环利用,但存在矿石转化率略低、焙烧温度高、成本偏高等问题,不适于大批量生产,需要提高钒转化率。
二、钒钛磁铁矿间接提钒
钒钛磁铁矿中由于钒是作为伴生元素存在的,因此钒含量比较低,虽然我国钒钛磁铁矿资源丰富,但钒含量普遍不高,一些钒含量较低的钒钛磁铁矿是不能直接提钒的。
我国大多采用间接提钒的方法,即以钒渣或含钒钢渣为提钒原料,主要以冶炼钢铁为主,钒作为副产品产出。
1.钒渣提钒
将钒钛磁铁矿通过电炉或高炉冶炼得到含钒铁水,再选择性氧化含钒铁水,使钒氧化进入炉渣中,得到了钒含量较高的钒渣,利用得到的钒渣进一步提钒。这种提钒方法在国内外广泛使用,较为经济合理。
目前,含钒铁水的处理方法主要有摇包提钒、雾化提钒、钠化钒渣法、转炉提钒等方法。
摇包提钒与雾化提钒由于综合指标低,提钒效果一般,现已不在发展;
钠化钒渣法是在铁水中直接加入碳酸钠进行吹炼,得到钠化钒渣,冷却后浸出提钒,但由于碳酸钠分解烟尘量大,浸出过程中脱磷困难等,需要逐渐完善工艺;
转炉提钒是一种成熟的技术,已被广泛采用,将含钒铁水兑入转炉中,进行顶吹、底吹或者复吹,使铁水中的钒被氧化而进入炉渣中,以达到钒铁分离的目的。
钒渣提钒工艺流程图
(1)钠化焙烧-水浸提钒:
钠化焙烧-水浸提钒是目前较为成熟的工艺,主要以钠盐(Na2CO3或NaCl)为焙烧添加剂,通过在回转窑中焙烧,将钒渣转变为水溶性钠盐,接着将高温焙烧熟料水浸得到含钒浸出液,然后加入铵盐,使钒酸铵沉淀析出,最后将钒酸铵热分解为五氧化二钒。
(2)钙化焙烧-浸出提钒:
钙化焙烧解决了钠化焙烧过程中的烟气污染,废水处理量大等问题,近年来逐渐受到关注。
将钙盐与钒渣混合焙烧,生成难溶于水的钒酸钙,再利用碳酸盐或稀硫酸浸出,浸出液净化后利用水解法沉钒,煅烧得到五氧化二钒。
钙化焙烧无有害烟气产生,炉料难以烧结,减小了钒渣中氧化钙的影响,废水可以循环使用,工艺成本降低。
(3)熔融钒渣氧化提钒:
钒渣焙烧工艺中将大部分钒渣显热都浪费了,熔融钒渣氧化提钒是在转炉吹炼钒渣后,向钒渣中直接加入钠盐并通入氧气,利用熔融钒渣的热量进行氧化,冷却后浸出沉钒获得钒产品。
该工艺减少了钒渣显热的浪费,减少了焙烧过程,降低了提钒成本,缩短了工艺流程,更加经济,缺点是操作要求高,工艺不太成熟。
(4)硫酸直接浸出法提钒:
近年来,硫酸直接浸出法也逐渐用于钒渣提钒,该工艺取消了氧化焙烧的过程,减少了焙烧设备投入,降低了能耗。
硫酸直接浸出法成本较低,操作简单,设备要求低,浸出液循环利用,工艺过程无有害物质排放,是一种对环境友好的提钒技术。
(5)亚熔盐法钒铬提取分离:
基于焙烧过程中的缺点,中国科学院过程工程研究所和河钢集团承钢公司利用亚熔盐非常规介质优异的物理化学性质,提出亚熔盐法钒铬提取分离技术。
由于亚熔盐介质对矿物具有很强的氧化分解能力,因此反应过程温度较低,可以实现钒渣中钒和铬的提取分离,且浸出率较高。
采用NaOH亚熔盐液相氧化法提取高铬钒渣中的钒铬,在反应温度220℃、NaOH浓度85%、碱矿比10:1、搅拌转速950r/min、常压通氧气流量1L/min、反应时间6h的条件下,钒、铬的浸出率分别达到95%和90%以上。
该工艺技术绿色环保,整个过程中无废气废液的排放,钒铬产品清洁分离,尾渣经过处理后返回钢铁冶炼程序,可实现工业固废资源化利用[15]。目前,该生产工艺已在河钢集团承钢公司投入运营,达到设计处理能力。
2.钢渣提钒
含钒钢渣产生于钒钛磁铁矿的炼钢过程中。将高炉或电炉产生的含钒铁水生蛆钒渣吹炼工序直接冶炼成钢,V2O5(2%-4%)进入钢渣中,钢渣作为提钒的原料。
该法无吹炼钒渣时的生铁损失,是一种新的处理方法。尽管含钒钢渣中钒含量较低,但仍比石煤中的钒含量要高,是很有利用价值的资源,可作为提钒的重要原料。
含钒钢渣中提钒主要有两种方案。一是对含钒钢渣进行火法冶炼,二是将含钒钢渣作为原料直接提钒。
(1)火法冶炼火法冶炼
可将钢渣返回烧结工序,也可对钢渣进行矿热炉还原冶炼。将钢渣中的钒富集到铁水中,吹炼得到高钒渣,作为提钒原料。
钢渣返回烧结:
将含钒钢渣作为熔剂加入到烧结矿中,钒渣同烧结矿一同进入高炉,钒可在铁水中富集,多次循环提高铁水含钒量再吹炼得到高品位的钒渣(V2O5含量30%-40%)。
此工艺在回收钒的同时回收铁、锰等金属,金属回收率提高,能耗下降。但是该工艺使磷元素在铁水中循环富集,提高后续脱磷难度,还导致烧结矿品位降低,因此,不宜大量使用。
钢渣矿热炉冶炼:
釆用矿热炉对钢渣进行碳还原冶炼,通过控制炉内的还原气氛将钢渣中的钒还原富集到铁水中,得到高钒生铁。高钒生铁吹炼钒后得到高钒渣,高钒渣处理提钒。
此工艺具有能耗低、资源综合利用,金属耗量小、钒回收率高的特点,但也会导致生铁中的磷元素增加,因此冶炼低磷钢时不宜采取此工艺。
(2)湿法提钒
现有的湿法提钒的工艺有很多,如直接酸浸、碱浸或加盐焙烧-浸出等,虽然根据实际情况处理方法有所差异,但是提钒原理都大致相同,先使钢渣中的钒溶解进入溶液中,再对溶液进行净化富集,最后从钒溶液中净化回收钒。
焙烧:将含钒钢渣与添加剂混合焙烧,例如食盐、苏打、石灰等,提高钒的回收率。通过高温焙烧将钢渣中低价态的钒转换为五价钒的盐,然后通过浸出,沉钒等工艺来回收钒,常见的焙烧方法主要有钠化焙烧、钙化焙烧、降钙焙烧、无盐焙烧等。
浸出:浸出是湿法提钒中重要的环节,主要包括酸浸、碱浸以及水浸。首先是酸浸,使含钒钢渣中的钒以离子的形式进入溶液中,再加碱中和,在弱碱性环境中将钒氧化为五价钒离子。
与传统的焙烧工艺相比无废气污染,无焙烧设备投入,减少了资源消耗,但是这种工艺流程也存在酸碱溶液消耗量较大,废液不便于处理的问题。
净化与回收:从浸出液中净化回收钒,现国内研究主要集中于离子交换法提钒与溶剂萃取法提钒,这两种方法提高了钒回收效率,缩短了工艺流程,减少了资源消耗,是今后研究的重点。
总结
钒钛磁铁矿直接提钒针对于高钒钛、低铁型钒钛磁铁矿,可以先提钒后回收钛、铁,但钒钛磁铁矿的钒含量普遍较低,这些矿一般不采用直接提钒的方法,国内外主要采用间接提钒的工艺。
间接提钒主要分为钒渣提钒与钢渣提钒,钒渣提钒是主要的提钒工艺。含钒铁水在转炉中吹炼得到钒渣,通常采用焙烧、浸出、沉钒来获得钒产品,但是传统的工艺存在废气、废水处理量大、能耗较高的问题。
随着工艺的优化,提出了新的钒渣提钒方法。
熔融钒渣氧化提钒减少了焙烧过程,降低了能耗,缩短了工艺流程;硫酸直接浸出法提钒减少了废气废水的排放,浸出液循环利用,是一种对环境友好的提钒技术;亚熔盐法钒铬提取分离用亚熔盐优异的性质,实现了钒铬提取分离,工艺绿色环保,废物资源化利用,是一种优异的提钒工艺。
钢渣提钒是新一代的处理方法,一是对含钒钢渣进行火法冶炼,二是将含钒钢渣作为原料直接提钒,需要继续优化工艺,提高钒的回收率。
在今后的发展过程中,智能控制、集成控制会成为工艺发展的方向,可以在线精准控制,准确预测,有利于产品质量的提升以及操作风险的降低。
同时,也要兼顾社会效益与经济效益,工艺流程向着绿色化、循环化、精细化的方向发展,高效低耗,环境友好,产品质量优异的工艺会是今后钒钛磁铁矿提钒的发展方向。
本文参考资料:钒钛磁铁矿提钒工艺综述、网络等
储能产业交流群
2021年全球电化学储能装机规模21.1 GW。其中,锂离子电池93.9%;铅蓄电池2.2%;钠基电池2.0%;液流电池1.2%;超级电容器0.2%;其它0.5%。到2025年,预计电化学储能增量将达到12GW/年,累计装机约40GW。在储能产业链中,各种电化学储能技术、新材料、先进制造设备、储能配套设施等都迎来了爆发式增长的机会。为促进储能产业行业交流,艾邦特建有“储能产业交流群”,欢迎业内人员加入。
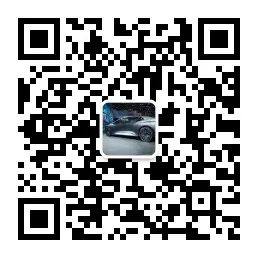
艾邦储能
更多储能资讯
扫码关注
原文始发于微信公众号(艾邦储能与充电):一文读懂提钒工艺全流程